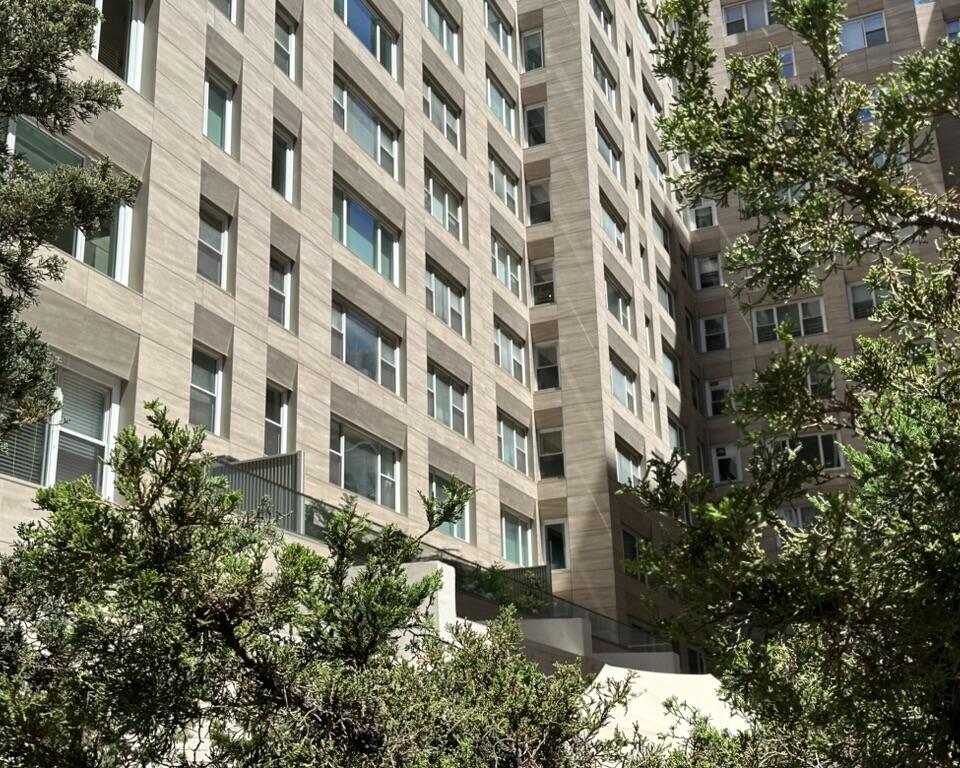
Out of the china cabinet and onto the façade
Cutting-edge porcelain tiles offer durability and low maintenance for Manhattan co-op
The façade of 201 E. 79th St., seen from the rear. Photo: Otis Miller
Sleek slabs form the outer layer of the new rainscreen system at 201 E. 79th St. These slabs are made of porcelain, a material New Yorkers might be more likely to associate with the delicate antiques in grandma’s china cabinet, or perhaps collecting dust in secondhand shops. But here, the old-timey material is giving this building a new lease on life.
The large, thin rectangular panels of porcelain that line the building were computer-printed with a pixelated pattern. Up close, you can see the half-inch, multi-colored squares; from a distance, however, the panels resemble the taupe shades of Indiana limestone — a classic building material in New York — making 201 E. 79th St. blend in with the surrounding landscape.
Countries in Europe and Asia have long used porcelain cladding for buildings. Now its use is expanding into North America, said Eugenio Megna, an architectural consultant and former vice president of sales and marketing at Fiandre, a subsidiary of Iris Ceramica Group. Megna, who has worked in the field for almost two decades, has noted “more acceptance and more curiosity” surrounding porcelain in the past ten years.
The panels used at 201 E. 79th St. were manufactured in a Tennessee factory owned by Iris Ceramica Group. Fiandre was chosen for the project after winning the bid for proposals put forth by members of the 201 E 79th St. co-op board.
These porcelain tiles were chosen for their durability. They’re impermeable to water, unlike older bricks, which are porous and susceptible to water damage after years of exposure. Since porcelain is less porous than brick, it is less prone to water damage and more efficient at trapping cooling and heating in the building — which is projected to also reduce carbon emissions.
Stefan Unger, a co-op board member who led the façade project, visited the factory in Crossville, Tennessee to learn about the production process, and saw the enormous kiln where the façade tiles are baked up close.
“Where they make these tiles is probably 12 feet wide, and three football fields long,” he recalled.
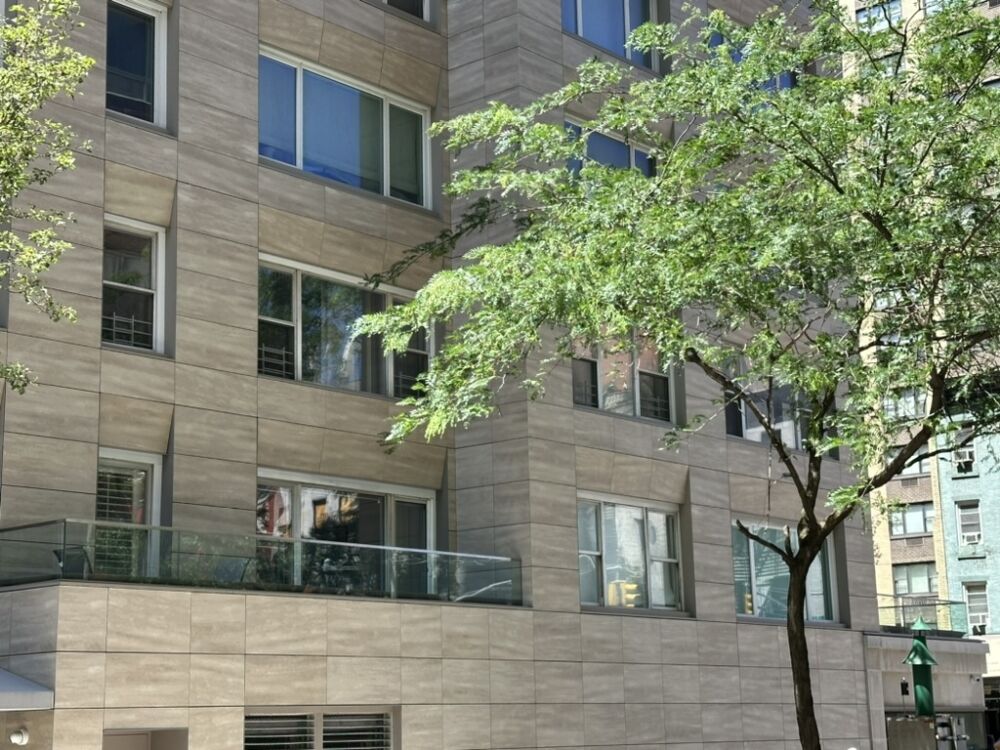
The porcelain tiles on 201 E. 79th St are made up of half-inch, multi-colored squares. Photo: Otis Miller
To make the porcelain, ingredients like clays and quartz are ground down into powders and blended with water, according to Megna. The mixture is allowed to dry, then pressed into molds custom-sized for a project — in the case of 201 E. 79th St., about two by four feet — and fired in a kiln for hardening.
Fiandre would not share the exact recipe for 201 E. 79th St.’s tiles, Megna said, but the plant that made them often uses post-industrial consumer content — reclaimed materials such as recycled porcelain from old sinks.
Once the slabs were made, the pixelated pattern — specified by Rogers Partners, the design architects for the new façade — was printed on. The panels needed to be clipped onto the rainscreen’s underlying aluminum grid, so a computer model showing the building in 3D was used to ensure that every porcelain panel ended up in the right place. This was especially helpful for tiles that would be placed vertically around windows, said Alissa Bucher, a partner at Rogers Partners.
The porcelain cladding should be low maintenance, she added. “From a cleaning point of view, it’s a dream, because you basically don’t have to clean it. The rain cleans it.”
The building has a stash of extra panels. If any panel on the rainscreen were to break, the damaged panel would be swapped out and a pristine one would be clipped on in its place.
So far, however, this hasn’t been necessary — 201 E. 79th St.’s porcelain panels appear to be holding up well.