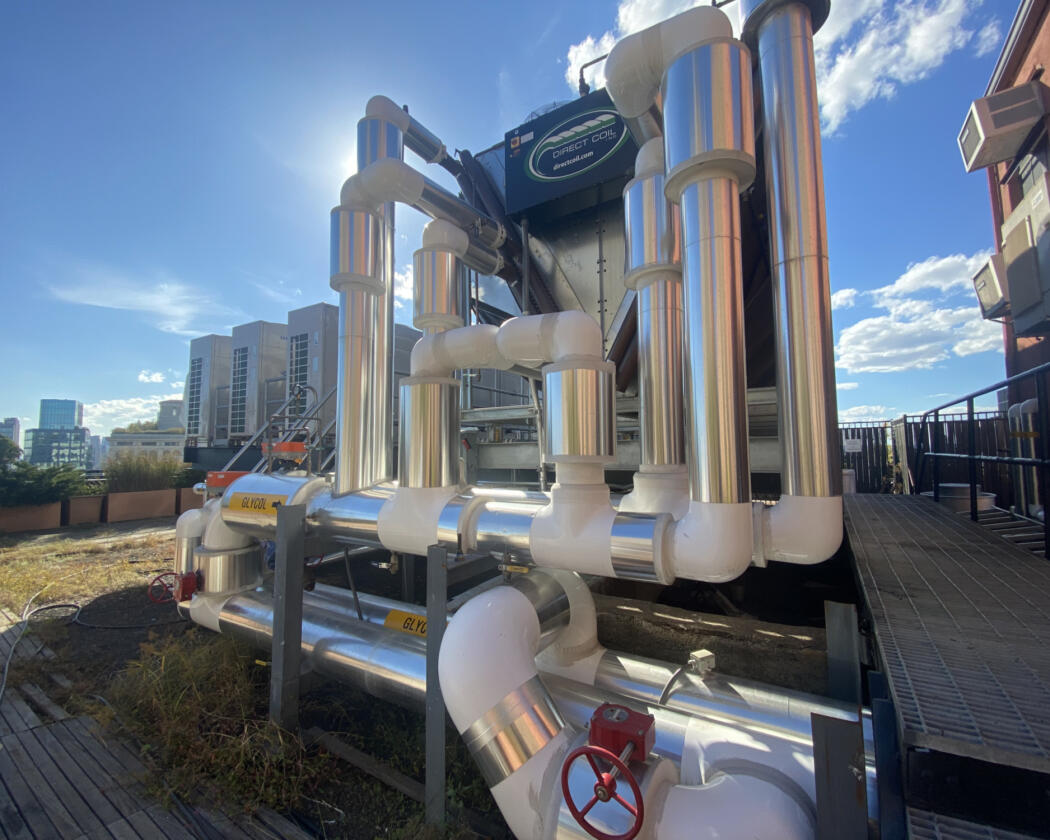
Installing heat pumps in a fully-occupied co-op
How this Manhattan building completed a major energy upgrade without disrupting residents’ lives
Photo: Mary Cunningham
For Eric Einstein, co-op board president of the International Tailoring Company Building, overhauling his building’s heating and cooling apparatus was akin to swapping out the engine of a plane mid-air.
“This is a fully occupied building with people living their lives, and we were changing the underlying technology that was powering their comfort,” said Einstein. “So yeah, it was tricky.”
Engineers had their work cut out for them. This was the first time Ecosystem, the company contracted for the project, had worked in a residential building in New York City. From the moment Ecosystem and the co-op signed the contract, the renovation process took close to two years to complete. During the construction phase, Ecosystem’s team spent roughly five days apiece in each of the 172 units, replacing the 34-year-old fan coils with brand-new hybrid water source heat pumps.
This meant having to work around the building’s nearly 300 residents.
“We needed our engineers in the building,” said Ben Milbank, senior project development engineer at Ecosystem. “This wasn’t something where you could be like, ‘Here’s the IKEA instruction manual on how you do this.’”
Ecosystem originally told the co-op board they would need five days of unfettered access to each person’s unit. But the board wasn’t thrilled with the idea of making people vacate their apartments entirely. So, after months of contract negotiations, the two sides struck a deal: Residents and their pets would leave their apartments from 8 AM to 5 PM for five days to allow subcontractors to get the work done.
The construction company also came up with what Ecosystem senior business development manager Jaime Pereira described as a “robust apartment protection regiment” to safeguard the units from damage and dust. In practice, that meant cordoning off the work zone in each unit with plastic curtains – no small feat for a building with 13.5‑foot loft ceilings.
“It made it a labyrinth for a lot of people, a plastic maze,” said Paul Cabana, a co-op board member who has lived in the building for 11 years.
To keep residents up to date throughout the life of the project, the board brought in AKAM, their property management firm’s project management group. AKAM handled all major communication efforts, a task too unwieldy for the volunteer board members to manage on their own.
Before the project launched, residents got an email detailing what to expect and a rough timeline of when each apartment was scheduled for its five-day visit. They also got a short reminder closer to the date.
The board simultaneously maintained its regular communication channels — a twice-a-year meeting with shareholders and a bi-monthly newsletter — to give tenants practical information and updates on major milestones.
Things didn’t always go exactly according to plan: There were occasional coordination issues, misunderstandings regarding the timeline, and delays in information sharing, said Levani Sidiani, former senior project manager with AKAM. In some cases, it took workers longer than five days to finish some units, which proved disruptive to some building residents.
“I think it took everybody by surprise just how unpredictable the experience could be, apartment by apartment,” said Cabana. The layouts in the building vary widely, which added an extra layer of complexity for the construction team.
Regardless, any hoops they had to jump through were well worth it in his eyes, and Cabana appreciated that everyone took their time to ensure things were done properly. “The scale of the upgrade so exceeded the hassle of installation,” he said.