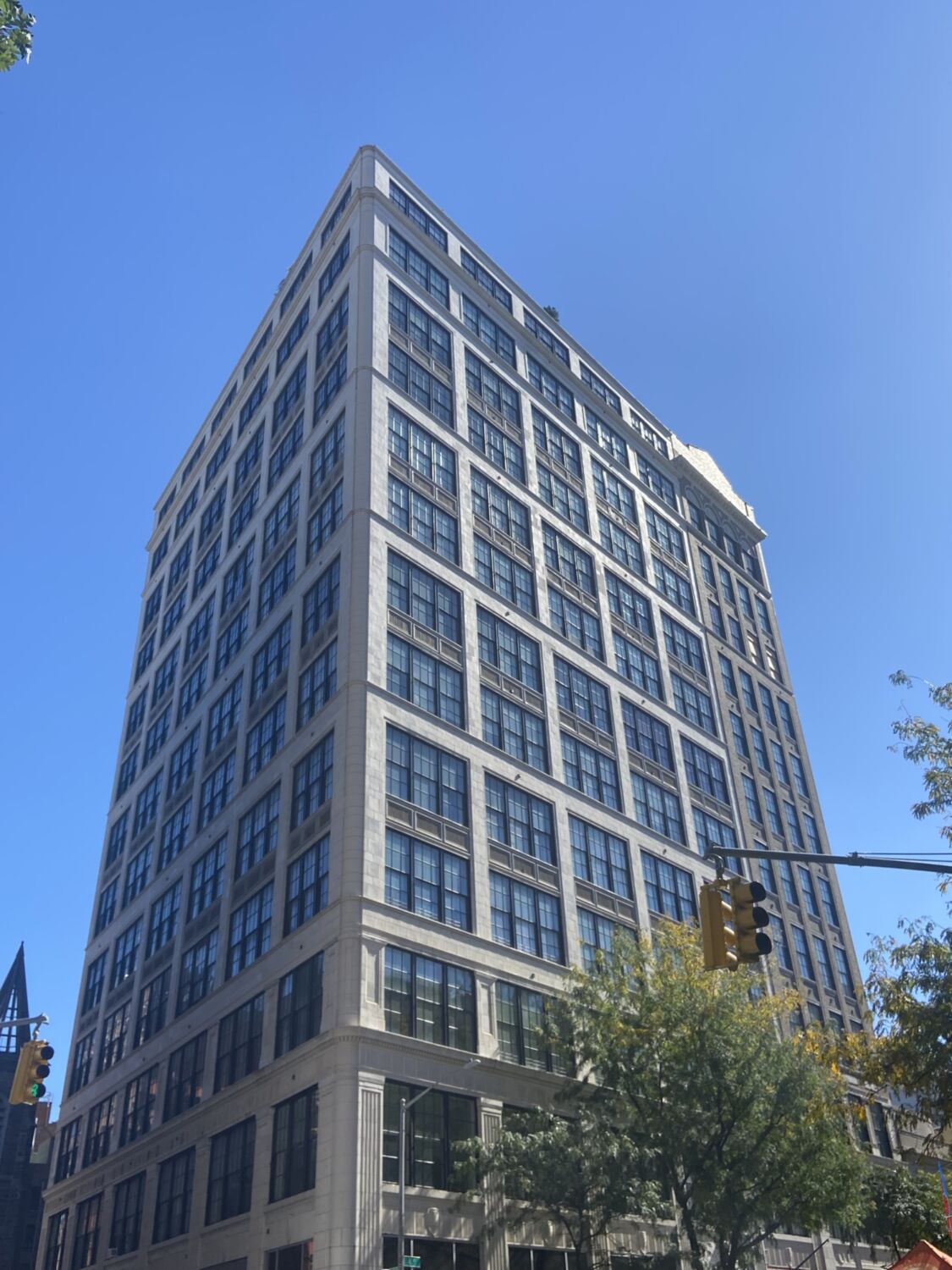
The International Tailoring Company Building stands at 111 4th Ave. in Manhattan. The former industrial building producing men’s clothing was converted into a residential loft co-op in 1980. Photo: Mary Cunningham
The International Tailoring Building set out to make their spaces more comfortable, and met LL97 regulations along the way
The International Tailoring Company Building, a 13-story residential co-op so named for its previous industrial life as a men’s suiting factory, sits at 111 4th Ave., just a stone’s throw from Union Square. With high ceilings and tall windows gleaming like a giant fish tank, the Manhattan lofts appear at first glance to be a spacious, modern building, offering comfortable living with apartments bathed in natural light. But the resident shareholders know better.
Comfortable and modern the building was not. Built in 1920, 111 4th Ave. still regulated its heating and cooling with technology from that era: A two-pipe hydronic system, which used hot or cold water to regulate temperatures. Under this two-pipe system, the entire building remained in either heating or cooling mode, preventing residents from controlling the temperature in their apartments.
“You end up with the sunny apartments being greenhouses, and the not-sunny apartments being cold on colder days,” said Eric Einstein, co-op board president.
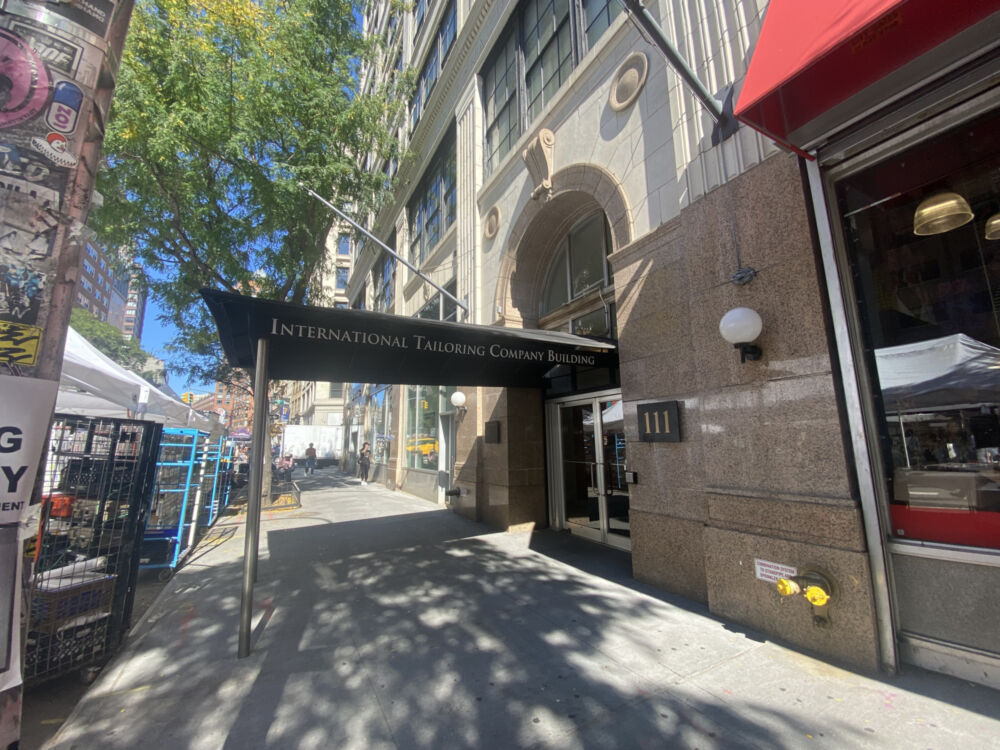
Exterior entrance to the International Tailoring Building. Photo: Mary Cunningham
The co-op owner-residents put up with these constant inconveniences for years until 2017, when one component of the HVAC system, the absorption chillers, was nearing the end of its useful life and needed replacement. The board took advantage of this situation to modernize the entire system.
A restauranteur by trade, Eric Einstein didn’t have the slightest background in HVAC engineering. But as board president, he nevertheless fell down the rabbit hole looking for the best technology to replace the building’s heating and cooling system to present to the board. What started as a quest for comfort would also come to help the building comply with Local Law 97 (LL97), the carbon emissions reduction law that came into effect in 2019, two years before the contract to start the building’s renovation was signed.
The Challenge
The road to success was laden with trial and error. Einstein quickly realized that despite all the guidance out there about energy efficiency retrofits, there wasn’t a one-size-fits-all approach to clean energy technology — he had to find the right system to meet the needs and constraints of his building.
Early on in his research odyssey, Einstein stumbled upon geothermal heating, a technology that harnesses the earth’s underground temperature to transfer heat, instead of a gas-powered system. This seemed like a good fit at first. Yet finding a knowledgeable contractor or engineer who could give him recommendations turned into a major hassle.
“You need someone who can work with your budget and your existing technology. So you need someone who has both financial savvy and technical savvy,” he said.
After months of setbacks and frustration, he finally found answers in Ecosystem, an engineering and construction firm with offices across the U.S. and Canada that specializes in improving energy systems in existing buildings.
The Roadmap
As soon as Ecosystem representatives met with Einstein and evaluated the building, they told him his idea of geothermal wasn’t feasible. 111 4th Ave.’s original design couldn’t support geothermal energy, as its old fan coils weren’t equipped to handle lower temperatures.
Instead, Ben Milbank, senior project development engineer at Ecosystem who worked with Einstein on the project, explained that they could repurpose the existing water-based system for a thermal network, a system that recovers and reuses energy to efficiently heat and cool the building, instead of drawing it from underground. Einstein presented this plan to the rest of the board, and everyone agreed it was the right direction to take.
Ecosystem planned to replace the fan coils in each unit that emitted hot or cold air with hybrid water-source heat pump units that would provide both heating and cooling all year round. They also planned to give residents an Ecobee thermostat to regulate their apartment’s temperatures at will.
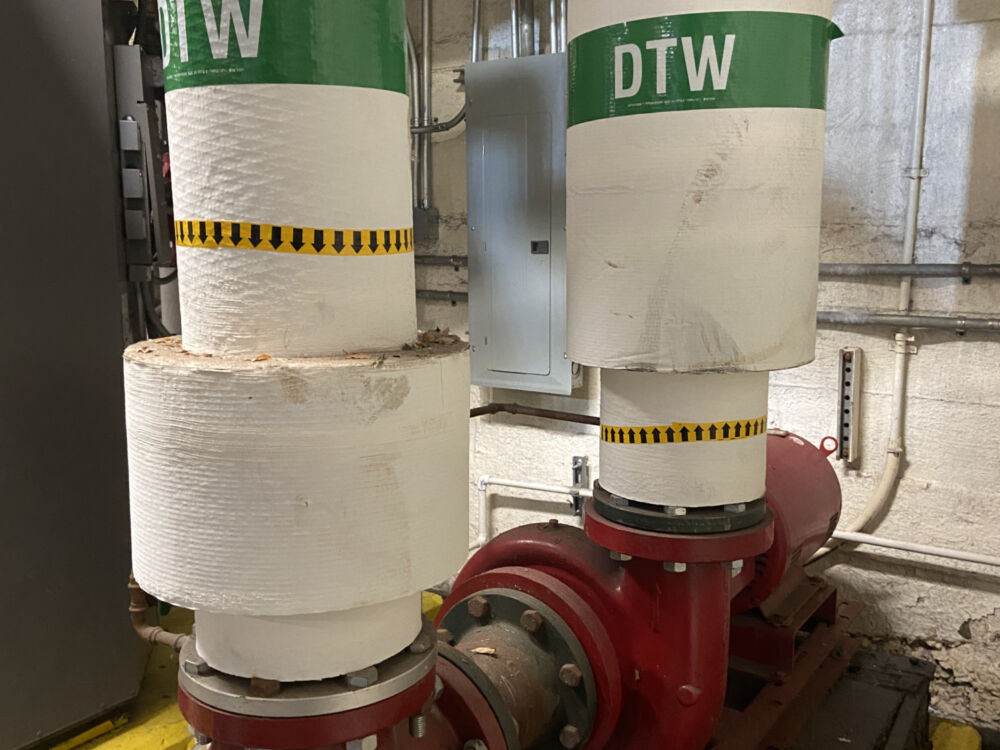
Photo: Mary Cunningham
“I was so excited. I was ready to volunteer to be a sample apartment if they needed it,” said Deborah Kadetsky, previous board member. She’d been living at 111 4th Ave. since 2006, and temperatures in her apartment could rise alarmingly high. “I was on a Zoom call, and all of a sudden my smoke alarm started going off. I panicked, and I realized it was because of the way the sun and the heat of the apartment was hitting it,” she recalls.
The renovations would require an investment of a whopping $9.3 million. Fortunately, the board of the International Tailoring Company Building had been preparing for over five years for such a big renovation.
In 2013, when Einstein took over as co-op board treasurer, the board had a list of all of the systems that would need to be refurbished, including the elevators, sidewalks, plumbing, and HVAC system. Einstein and the board preferred to prepare for these inevitable expenses, rather than wait for disaster to strike, so they implemented a three percent annual increase to shareholders’ maintenance fee. This helped them build a big cushion of savings by the time they signed the contract with Ecosystem in 2021.
“If you’re spending money reactively, you’re just going to be throwing money down the drain,” said Milbank.
By then, LL97 had passed, and the thermal network project qualified to receive financial incentives for its development.
Originally, Ecosystem had planned to install new gas boilers to power the entire system and tackle decarbonization down the road; however, if they went in that direction, they would risk fines for exceeding emission standards set by the new law. So, instead, Ecosystem recommended they install a series of electric heat pumps on the roof, using only two new gas boilers to supplement the heat pumps during the coldest days.
By choosing this pathway, they secured a handful of incentives from NYSERDA and Con Edison, and qualified for an Inflation Reduction Act Thermal Storage tax credit for thermal storage that helped them fund the project, reducing costs by $3.28 million. In the end, they paid $6 million out of pocket.
The Project
After a very meticulous back and forth between the Ecosystem and Einstein, who took his time to research the technical specifics to make sure the project would fit the building’s needs, the construction work started in May of 2022.
The work comprised three phases that ran almost simultaneously: While one team worked on replacing the boilers and all the mechanical systems in the basement, another would replace the systems in each of the apartments, and a third team would install the heat pumps on the roof.
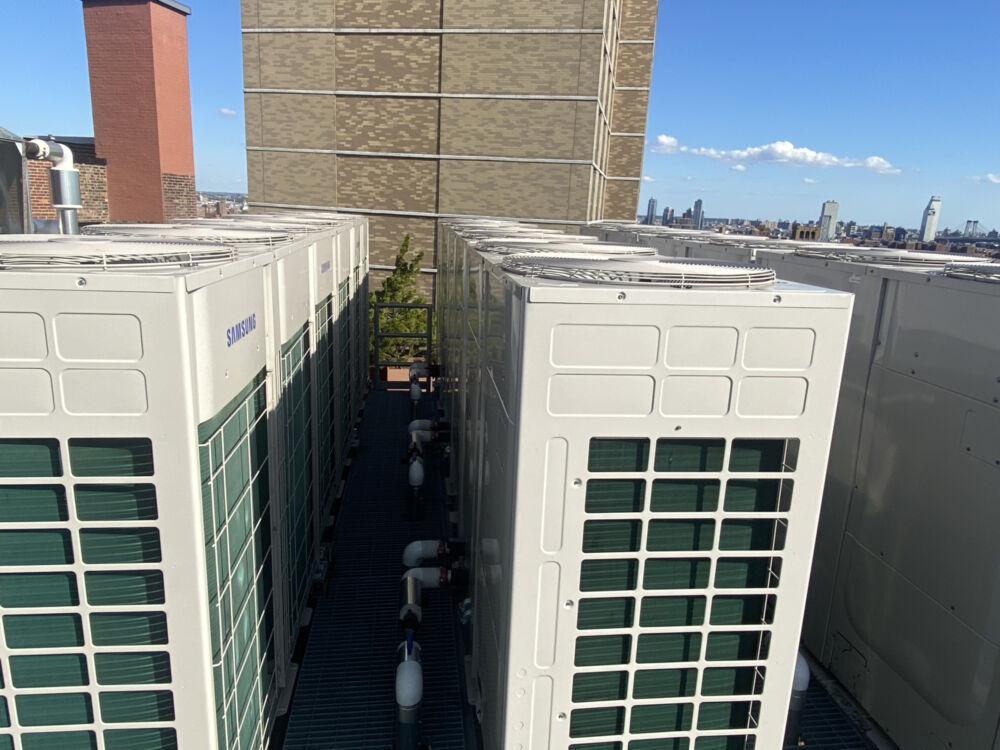
Air-source heat pumps installed on the roof of the building. Photo: Mary Cunningham
While some shareholders chose to leave during the week-long renovation process in their individual apartments, others stayed to face the mess. The board, in partnership with the property management firm AKAM, made sure that everyone knew about the project with ample time in case they wanted to stay elsewhere, but they also made sure that the construction crew found ways to work without needing to kick people out, protecting the apartments with plastic when necessary.
By June 2023, the renovation was done, leaving residents with complete control of temperatures in their apartments.
Now during hot seasons, Kadetsky says, she turns off the AC when she leaves, and just as she’s riding the train home she turns it on again remotely via mobile app, so she can arrive at a cooled-down apartment. “It’s wildly upgraded from what we had in the past,” she said.
Still, she wishes someone had given her and the rest of the co-op residents a complete tutorial on how the new thermostats work. “From my perspective, there wasn’t a lot of proactive information about what this thermostat is, how it works, or how to change your settings,” she said.
It is unclear exactly how much the building will save in carbon emissions because of the new system, but the engineers project it will save up to 80 percent of onsite emissions, which positions the building to comply with LL97’s goal of reducing greenhouse gas emissions by 40 percent by 2030.
The building is not fully weaned off of carbon-based energy, as it still has gas boilers to supplement the heat pumps. But the mix of energy has shifted greatly towards electricity, and the building overall uses less energy to heat and cool apartments, because the electric heat pumps are more efficient than the previous fossil fuel-powered systems.
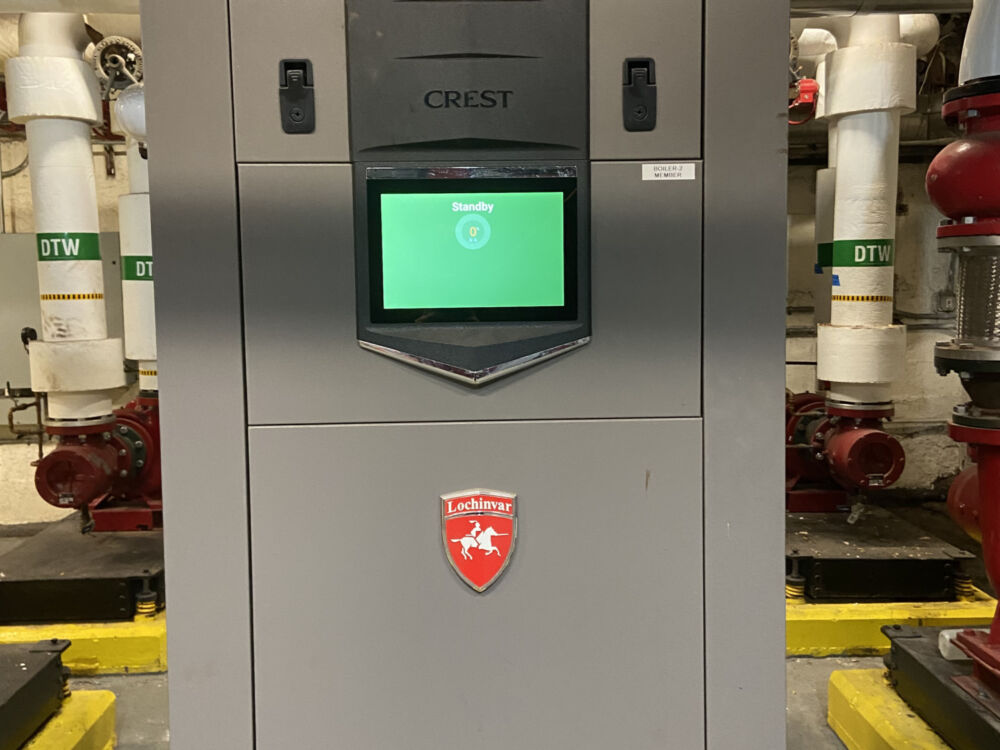
One of two new condensing gas boilers in the basement of the International Tailoring Company Building. When the heat pumps on the roof can’t heat up the water in the thermal network enough, these boilers kick in as a backup source of energy. Photo: Mary Cunningham
This project is an example of “hybrid electrification,” according to Stephanie Schwartz, director of marketing communications for Ecosystem. She says one big takeaway from 111 4th Ave.’s retrofitting is that buildings don’t necessarily have to eliminate everything that emits carbon to meet decarbonization goals.
The International Tailoring Company Building is a work in progress. Residents will be responsible for replacing their old windows, which sometimes have problems opening and closing, and the board will soon begin renovations to the roof.
Yet overall, residents feel proud of all the work they put into the building. For his part, Einstein doesn’t regret a second of the hours he spent researching. “Don’t be afraid of starting somewhere and asking questions,” he said. “Even if you run into a bunch of walls at first, eventually, hopefully, you come to something that will work.”