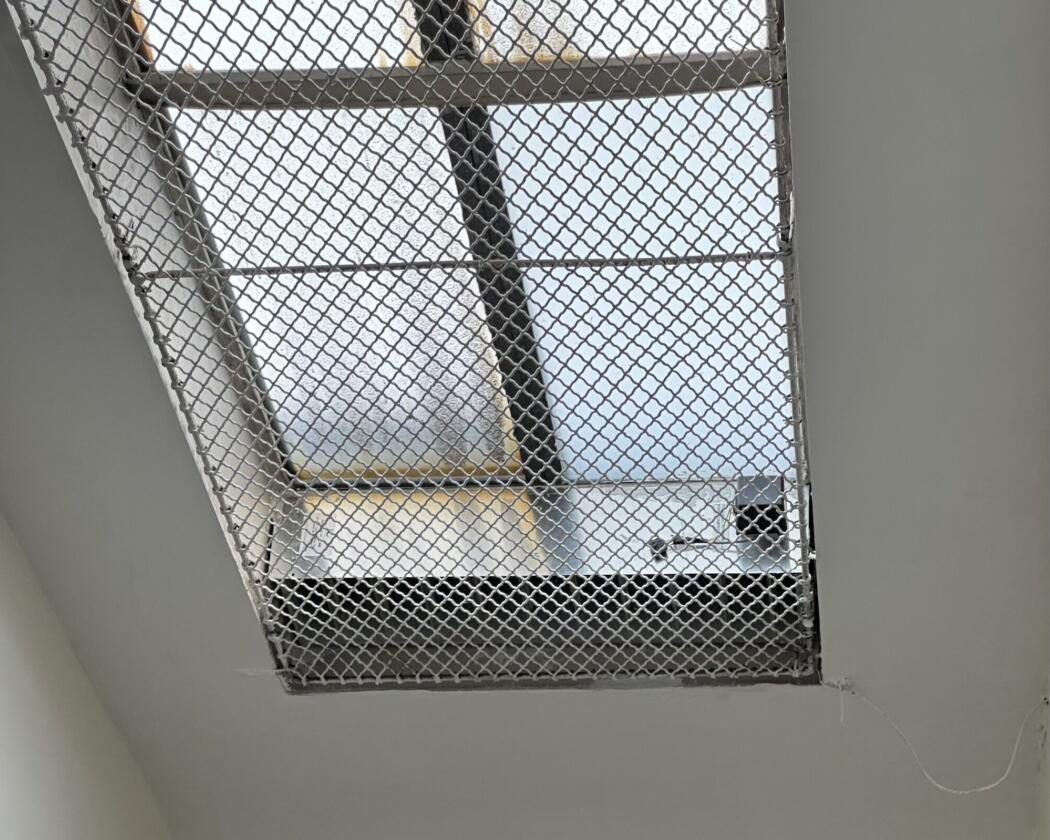
Sealing in the benefits of energy efficiency
Project designers explain why air sealing is a crucial component of any energy efficiency project
A view of the co-op’s ceiling, now better sealed against air leaks after professionals performed a blower door test. Photo: Otis Miller
When asked for advice on heat pump installations, energy efficiency expert Tom Sahagian doesn’t hesitate — he recommends air sealing before anything else.
“Even if they have no plans to convert to a heat pump, they should do air sealing,” he says.
In older buildings especially, air can surreptitiously leak from all types of places, from a gap between a window frame and the wall to a baseboard that isn’t caulked along the bottom edge. Air sealing is the process of finding and closing those gaps. This not only improves living conditions for residents, but also lowers the heat load — the amount of heat necessary to make a space comfortable.
“You don’t want the air sneaking around,” said Sahagian.
Sahagian decided well before the heat pump installation at the UWS building that participated in the Taitem Engineering pilot project that air sealing was essential to its overall success.
This process started with what’s known as a “blower door” test: A machine that can be fitted to a door frame pressurizes or depressurizes a building, revealing gaps that air can seep through. It’s a method more commonly used in single-family buildings, but can also work for multifamily buildings.
“Exaggerating leaks makes them easier to find, and then you can do the work of plugging them up,” Sahagian said.
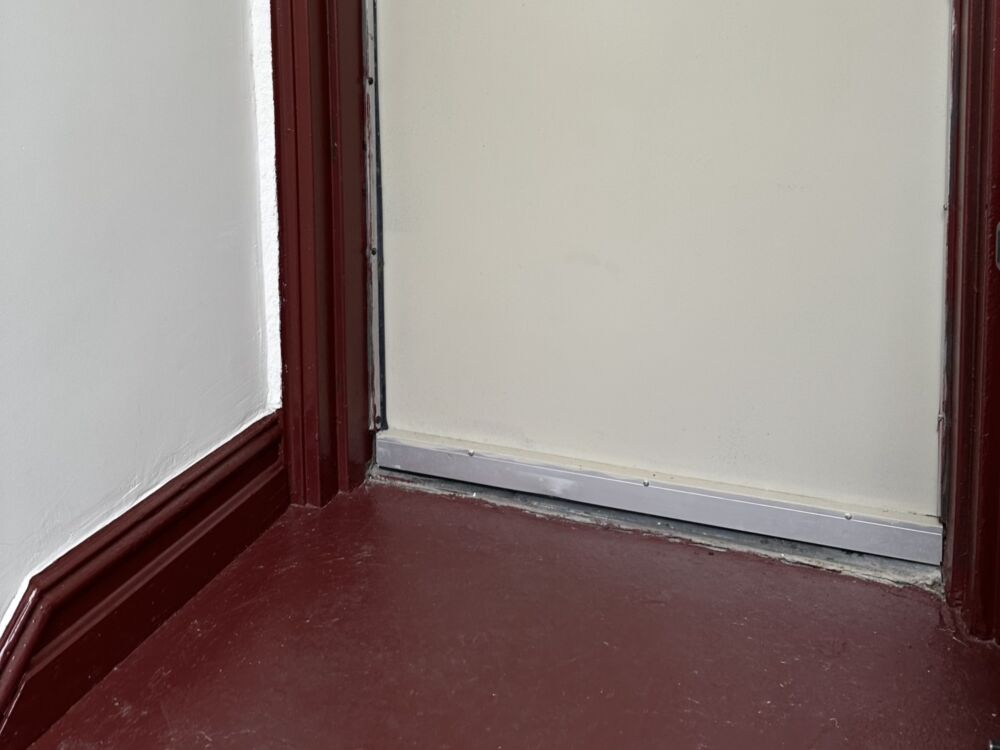
The roof door, now better sealed against air leaks with weatherstripping. Photo: Mary Cunningham
Taitem Engineering performed two rounds of these tests: One in June 2020, pre-retrofit, and then another in February 2022, post-retrofit. Once the leaks were identified, Sahagian and a handyman hired by the building did air sealing on the front door, the roof door, the basement doors, and a selection of apartment doors for residents who opted in. This involved adding weather-stripping tape made of synthetic rubber and aluminum around the door frame and door sweeps to close the gap between the door and the floor, a process known as compartmentalization.
Sahagian and the handyman also sealed a defunct dumbwaiter shaft, which had been acting as a pipeline for warm air, and two windows in the basement.
The cost of the air sealing, which came in at about $12,000, was subsidized by Daikin, the heat pump company behind the pilot project.
The process worked so well for resident Lisa Harrison that it not only blocked cold air but also kept out unpleasant odors, like the strong-scented floor cleaner used in the hallways. “Even a smell didn’t come in,” she said.
While the co-op waited until after the Daikin heat pumps were installed to perform air sealing, Jon Hacker, Daikin’s former Energy Efficiency Business Development Manager, said that best practice is generally to do it in the reverse order: “If you reduce the load of the building, we can now appropriately size a heat pump for that load,” he said.
Along with air sealing, the building also added insulation to apartment walls, the basement, and the roof gradually over the years. They hired Brooklyn Insulation & Soundproofing, a company that specializes in cellulose insulation in older buildings, to do the job. For their projects, the company uses cellulose made of shredded recycled newspapers and magazines.
The pilot study by Taitem Engineering that the building participated in found that fortifying the building’s envelope went a long way in increasing thermal comfort for residents. Umit Sirt, an engineer at Taitem, also said that apartment temperatures remained more consistent throughout the building, and more even across different floors. As a result, the study suggested that peak demand for electricity was “lowered considerably” due to envelope upgrades.
Amalia Peña, a resident on the top floor who has lived in the building since 1987, said she’s noticed a big difference since the insulation was added. Sometimes it’s so warm, she doesn’t need to turn on the heat pumps at all. “It was a very good investment,” she said.