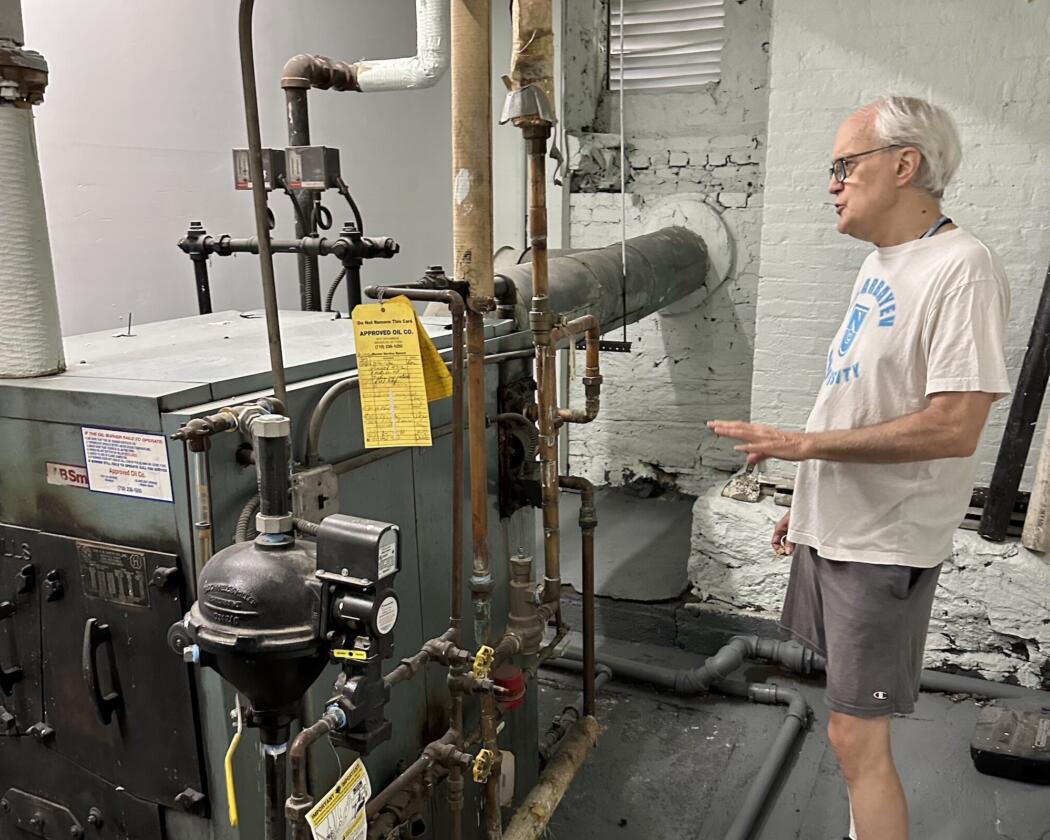
Tips from Tom Sahagian
An energy aficionado offers advice on how to make the switch to more renewable technology
Tom Sahagian explaining — what else — a boiler. Photo: Otis Miller
Throughout his 40-year career in energy efficiency, Tom Sahagian has gotten up close and personal with boilers plenty of times. “I never met a boiler room that I didn’t like — even the really gross ones,” he said.
Despite attempting to retire almost 10 years ago, Sahagian still finds himself in the thick of all things energy as a part-time advisor for NYCHA and adjunct professor at Columbia University’s School of Professional Studies. Yet these days, he finds himself taking on more electrification projects than boiler work.
He developed the idea for a pilot project for heat pumps in multifamily buildings, which brought him to the doorstep of a five-story HDFC co-op in Manhattan. Here, he teamed up with resident Lisa Harrison, as well as companies Taitem Engineering and Daikin. The pilot was a lesson in executing what Tom believes will be the future for many of New York’s buildings in coming years — making the switch from fossil fuels to electric solutions with good energy-efficiency practices, such as installing heat pumps and air sealing.
Here are a few lessons learned from the project, as told by Sahagian.
1. Expect some glitches
When it comes to heat pump installation, there’s no one-size-fits-all approach. As Sahagian experienced during the co-op’s project, customized, DIY-type solutions also require some trial and error. Running into issues is to be expected — and this project was no exception.
Materials arrived late due to COVID supply chain issues, and various hiccups arose during the installation process: Contractors didn’t properly seal the condensate lines on the side of the building at first, causing water to leak into some apartments during a big rain storm.
“People need to know that these things can happen so they can guard against them if they decide to go this route,” Sahagian said.
Then there were the smaller, aesthetic issues. Some of the electrical and refrigerant lines were too far out of reach to be concealed by line-hide, a protective plastic cover for wires, so they were left dangling off the side of the building. A smattering of condensate drain pipes can also still be seen poking out of the brick façade, albeit on a side of the building not visible from the street. These physical blights, while minor, were an unplanned remnant of the installation process.
Most importantly, however, nearly five years after the installation, everything is operating as it should be. “Overall, the units themselves have worked really, really well,” Sahagian said of the Daikin heat pumps.
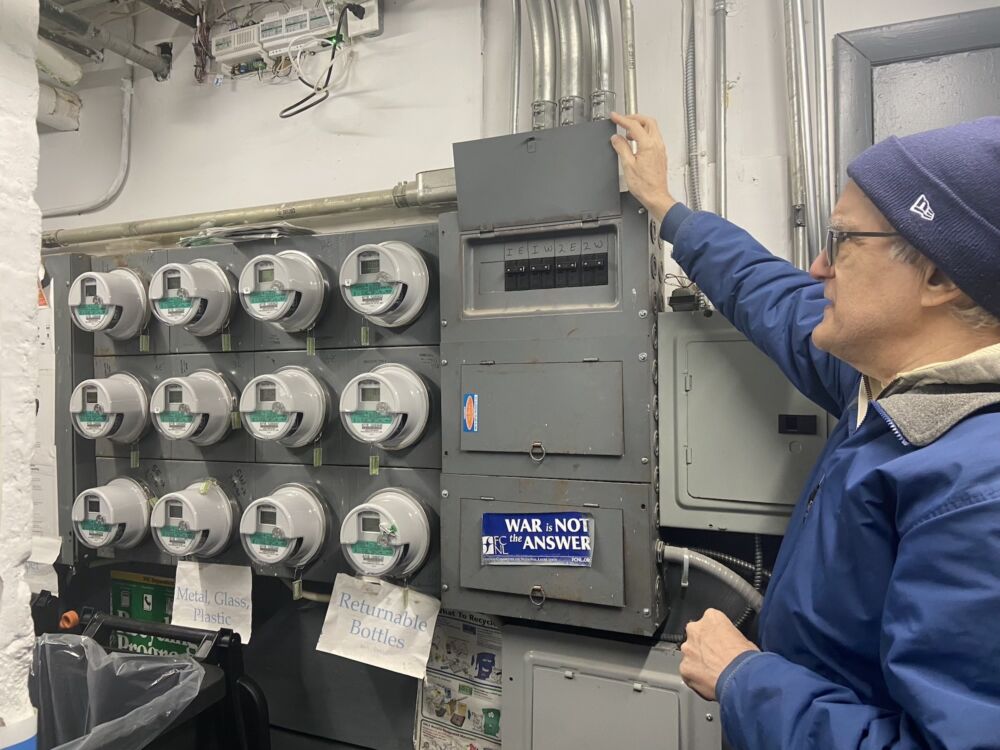
Tom Sahagian in the basement with the building's electricity submeters, which now measure the electricity used by their new heat pumps. Photo: Mary Cunningham
2. No need to nix everything all at once.
Keeping an old oil-fired boiler may seem contrary to the goals of Local Law 97 (LL97). But not everything needs to go out the window all at once, especially if it’s working the way it should.
Some shareholders in the building advocated for the boiler to be replaced, fearing it was on the verge of collapse due to its age. But Sahagian says it’s not age that dictates whether a replacement is needed, but rather how much corrosion the boiler has been forced to undergo.
A more piecemeal approach to going green is often best, particularly if cost is a concern. That was the case for this building, which is still using the 40-year-old boiler in the basement to supply domestic hot water while shareholders build up reserves to invest in a hot water pump. In the meantime, the new Daikin heat pumps provide heating and cooling, and the building has still lowered greenhouse gas (GHG) emissions associated with heat and hot water by nearly 60 percent — proof that buildings can meld the old and the new while still lowering their carbon footprint.
“So, seeing as how Local Law 97 wants you to cut your greenhouse gasses [significantly] by 2050, getting rid of 60-odd percent of what you used for heating is pretty huge,” said Sahagian.
3. Weigh which technology is right for you — even if that means waiting.
As heat pump technology evolves, Sahagian advises buildings to weigh their options. Window heat pumps, which sit like a saddle over window frames, are less intrusive, easier to install, and cheaper than other options because they don’t require trade labor to open up walls and run lines, Sahagian said. These units can be plugged into a regular wall outlet, and present a much lower risk of refrigerant leaks.
In fact, Sahagian said that his decision to develop a model for a window heat pump is the “logical outcome” of his experience with the Taitem Engineering project, where the installation was at times messy and noisy.
Now, as a part-time employee for NYCHA, Sahagian is testing the scalability of these window units with a pilot project in partnership with the housing authority. They’ve already installed 72 Midea and Gradient units at its Woodside development in Queens, and are gearing up to install 144 more Midea heat pumps in the Summer and Fall of 2025.
“We hope that buying a lot of these things will maybe induce other manufacturers to come into the market,” he said.