
“If we could do it, anyone could”
A Q&A with two cooperators from one of New York City’s original self-managed Finnish co-ops, who coordinated efforts to tune up their ancient boiler and patch up leaks in the walls
Samara Doucette, left, and Mike Weiss, right, were both on the co-op board at Sun Garden Homes in different eras. Photo: Hannah Berman
Many New Yorkers are familiar with the cooperative home ownership model, otherwise known as the co-op. Yet even those who know co-ops well might be surprised to learn that this model first appeared in the US in Brooklyn’s Sunset Park, at the hands of Finnish immigrants looking to lower housing costs by pooling their resources.
Sun Garden Homes, located at 637 – 661 41st St., is one of those 25-odd original Finnish co-ops, built in 1926 and owned and managed collectively ever since. The ethos at Sun Garden Homes has always been to do it yourself, so when the building started showing some severe wear and tear, several of its cooperators banded together to figure out what they could achieve: They dove into fixing up the boiler, overcladded the North wall, and patched up leaks, helping the co-op retain energy and run more efficiently.
Two of those cooperators were Mike Weiss, who was the co-op board president from 2018 to the middle of 2020, and Samara Doucette, who took up the helm later on in 2021. Weiss works in solar energy, while Doucette works in hospitality sales; they both had to develop deep knowledge of their building to be able to take the lead on these repairs. They welcomed Skylight onto their roof one sunny March afternoon to chat about what they accomplished.
This interview has been edited and condensed for clarity.
Skylight: Samara, start us out by telling me about this building and your relationship to it.
Samara Doucette: I moved here in 2017. When I came in, obviously I knew the building was self-managed, but I didn’t really know what that meant. Mike [Weiss] was on the board already. Early on, we had a leak behind the walls, and Mike had to come in while we were on vacation and plow into the wall to fix a leak before it became something much bigger. There was already a plan for redoing the façade, which Mike had started and was leading. I knew I would volunteer at some point, but during the pandemic, my work slowed down a little bit, so I was like, well, this is a great opportunity to do my service — without realizing what I was undertaking.
And how about you, Mike?
Mike Weiss: I moved in 2008 with my partner Rachel, who was pregnant at the time. We liked the whole vibe of the building and how people took an active role in taking care of it, and that it was inexpensive. It just agreed with my sort of personality — I like to do things myself.
Jan, [a neighbor] who probably moved in 10 years before I did, he was sort of a house plumber, in a way. He was a superintendent at a building in the city, but he did a lot of work with the boiler system here. Then there was another guy who did carpentry, and another contractor. They sort of did small roof repairs here and there and just kept things going. They lived in the building.
So, you’ve done a ton in this building. I see solar panels on the roof with us — when did you get those?
MW: We started back in 2010 – 2011. We had trouble getting people on board initially, but it paid back in a couple of years, generating revenue for the building.
SD: When I joined, we came in May, and the loan payments for solar were paid off by September. It was bite-sized enough for members to agree to. We were new tenants, thinking, “This is great, we get the benefits of solar, but we only paid for it for three months, through the purchase price of our home.”
MW: Between solar and sub-metering, we make around $20 – 25,000 a year.
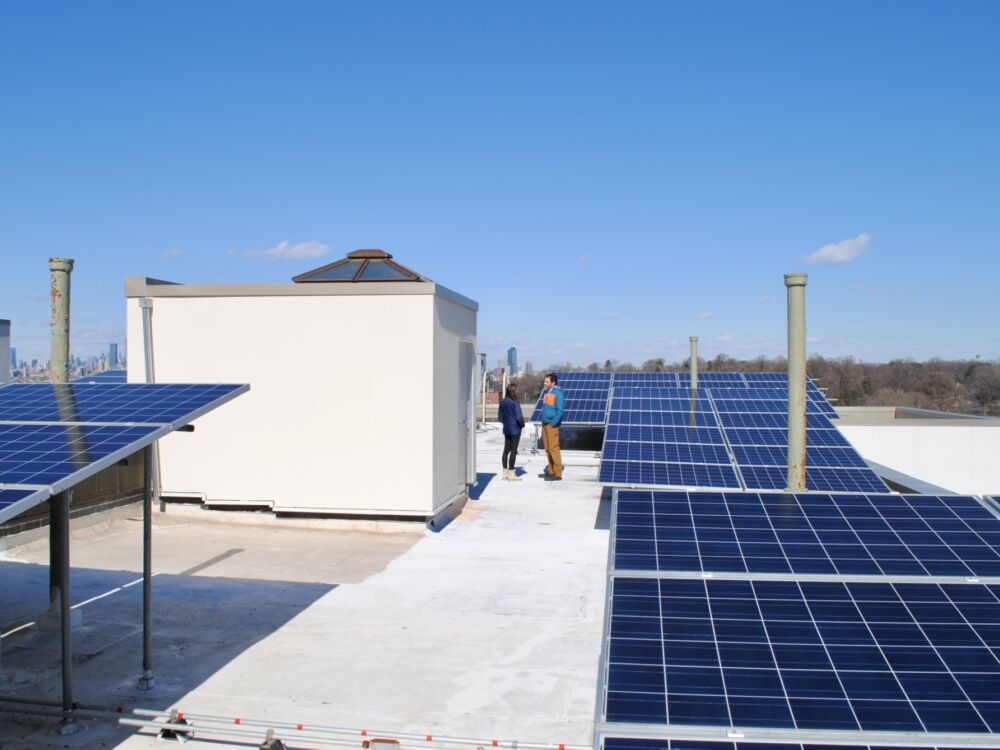
Solar panels on the roof at Sun Garden Homes. Photo: Hannah Berman
It sounds like you’ve tackled a lot. Tell me about the boiler first. When did that work start?
MW: It’s ongoing. Before I moved in, part of the shell rusted through, which fueled concerns that it would fail. That’s a chronic issue in a lot of these buildings. One of the local laws that just kicked in was Local Law 87, which was a benchmarking local law that mandated measuring water and energy use in the building. We had to comply with that, so we ended up hiring Bright Power, which was a consulting firm at that point. They came in and did a study of the boiler and gave us recommendations for how to vent the steam lines, just a bunch of prescriptive things, which we ended up doing.
The expectation was the boiler was going to blow. Whenever we had an annual meeting, that was the message — “Oh, the boiler, it’s on its last leg.” It was probably about 20 – 25 years old at that point, but I was determined just to keep it going as long as we could. Local Law 97 hadn’t happened yet, but it seemed like a rash thing to replace the boiler in kind without thinking about improving the system. It’s a simple machine, when it’s demystified — basically a big teapot, boiling water.
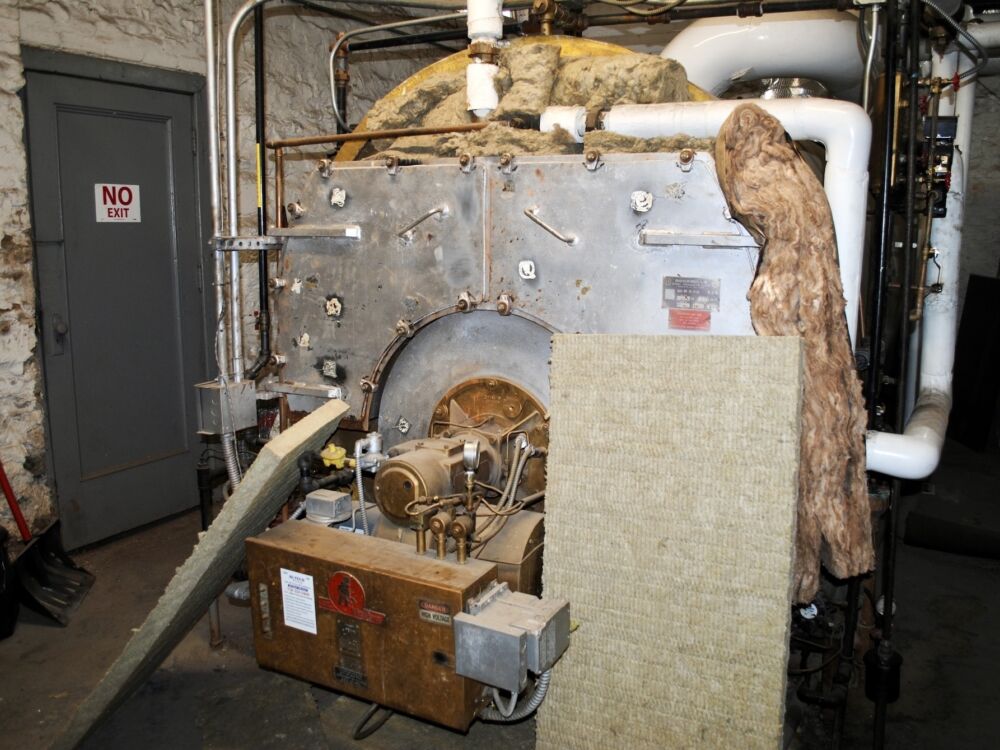
Sun Garden Homes’ boiler — “Basically a big teapot, boiling water,” according to cooperator Mike Weiss. Photo: Hannah Berman
How was Local Law 97 on your radar?
MW: [Our neighbor in the co-op and energy expert] McGowan Southworth was in energy in 2012, and I work for Solar One, a nonprofit doing solar. We were really into it. We were dealing with Chris McGinnis and others in this energy group. It wasn’t just a hobby, more of an interest. [Local Law 97] was definitely top of mind.
So, once you realized you could repair the boiler instead of replace, how did you go about that?
MW: Jan, our in-house plumber, replaced many rusted condensate lines over the years, but we finally got ahead of it. We also turned down the firing rate, which had been running way too high. Mechanics would compensate for a poorly performing system by just turning up the pressure, which just causes overheating.
SD: You also recalibrated things. We have some apartments that overheat, and some apartments that underheat. What was that work you did with the venting?
MW: Bright Power helped with that. They measured how long heat took to reach different parts of the building and recommended venting adjustments — installing a main vent in the area furthest away from the boiler, to push out air faster. Also, there’s an air vent on everybody’s steam radiator, and those air vents might have been painted over, or might not work, so we made a very concerted effort to just make sure that the steam system was breathing and operating properly. That helped a lot.
SD: Later, when I took over boiler maintenance, we updated the control panel, which was a really ancient piece of equipment. We did a lot of cleaning and tuning, replaced gaskets, and cleaned the chimney. Smaller, nuanced stuff. I learned way more about boilers than I ever thought I would in my entire life.
MW: Me too. My dad once told me, “You should really learn about boilers.” He was a doctor, so I thought that was the weirdest thing to say — but now I get it.
SD: And the expert we worked with on a lot of the boiler stuff, when he inspected our overall system, he said we were running at an 89.3 efficiency rate. That’s excellent, considering that our boiler goes back to the 80s. I like that number! That’s a good number. It shows you can run a building on really old equipment and it’s still efficient.
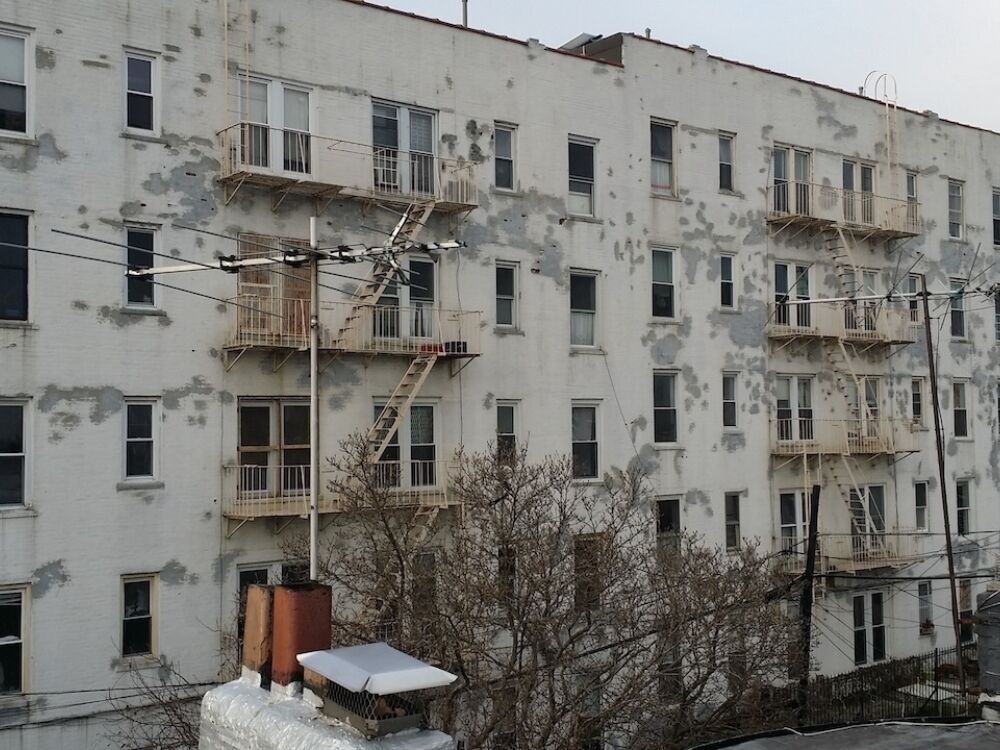
Pre-2019 image of Sun Garden Home’s leaky North wall. Photo: Provided by Mike Weiss
Alright, now let’s talk about the façade overcladding project. Was this a Local Law 11 upgrade?
MW: No, Local Law 11 applies to buildings over six stories tall, so we didn’t have to comply. The issue was that we had chronic leaking on the north wall. The north wall became a thing — the North Wall.
The standard treatment for that was that you’d have a masonry contractor come in, and they’d be like, “We’ll just throw a coating over the whole thing.” But if you do that, you’re in this maintenance schedule where you’re always going to be doing repairs every five years. And that’s costly in itself.
MW: We looked at [different types of] overcladding. The standard system is EIFS (Exterior Insulation and Finish Systems) — it’s an insulation layer covered with synthetic stucco. It’s common in Europe and commercial buildings here. The beauty of that was that it would very efficiently cover the exterior of the building, keeping the freezing surface away from the brick, so you no longer have any freeze-thaw.
SD: As we were doing brickwork, we found lots of little pockets where there were more leaks and it was usually because the mortar was compromised.
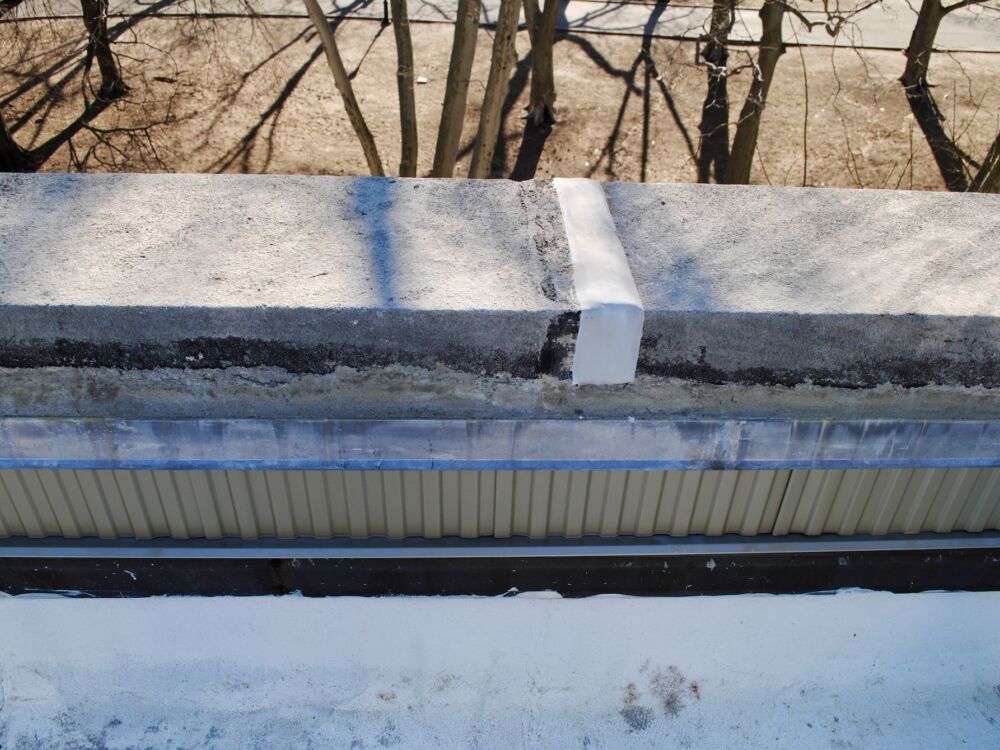
As part of the façade project, metal cladding and coping was installed at pressure points to prevent water from seeping into cracks. Photo: Hannah Berman
MW: Exactly. Masonry buildings of this era constantly deal with deteriorating mortar, lintels, and leaks. EIFS prevents that. We formed a North Wall Committee to explore options, and eventually, we brought in architect Chris Benedict, whose whole jam is energy-efficient retrofits. She convinced several of us in the building to do the [EIFS] overcladding system, because it was economical and would save a lot of energy. Eventually, Samara and [another resident named] Alexander almost became the general contractors.
SD: Alexander is an architect, he lives in the building, too, and his expertise was invaluable. Without him, this wouldn’t have happened. It was the right decision to push forward, but it was messy.
MW: This became a classic example of scaffolding that just doesn’t go away. We did the first step of EIFS and got the wall solid enough, but then COVID hit. And now we were committed — we were spending $55,000, $60,000 a year on scaffold rental.
SD: The board tried to find solutions, but COVID threw things off. When I joined, we had to start from scratch — there were insurance issues and no real contractors lined up. So Alexander and I took charge, found a new architect, and reevaluated the project to ensure we stayed on course.
We could have just said, “No, we’re not going to do EIFS.” We had a coat on and we could have just done regular cladding, but I think we were afraid that the same problems would continue to persist. And also, we wanted to honor the decisions that had already been made and see this through, and it was going to help us with Local Law 97.
When did it close? Is the infamous North Wall done?
SD: The wall is done! All the east, west, and north walls are done, and all the lintel repairs are finished. The only issue left is that the yard lights they installed are glaring into people’s apartments and disturbing our neighbors. They’re going to install an alternate light soon, and once that’s done, we can close the project. We’re really in the final stage.
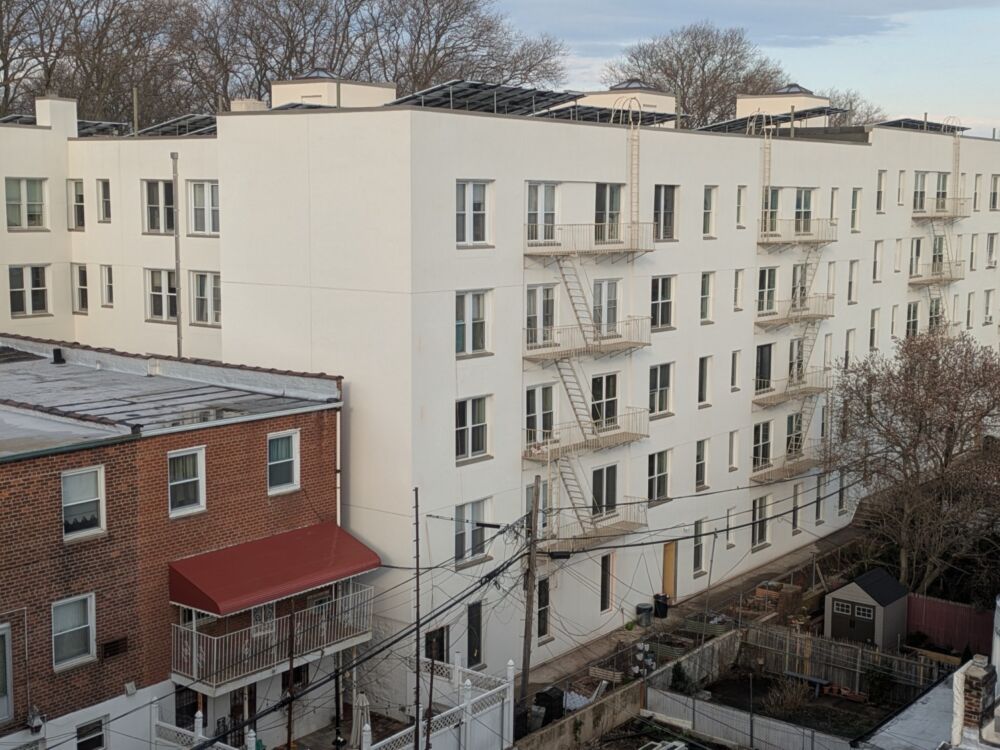
Residents at Sun Garden Homes are no longer having issues with the North wall after recladding it with EIFS. Photo: Provided by Mike Weiss
Congratulations! Can you circle back a little to the financing and how you made that work?
SD: Our treasurer at the time, Seth Pearce, really took that on — thank God. He got different options from various banks. NCB was one of them. We presented the whole package of the work to the membership in a special meeting, explaining everything we were hoping to do, including the loan amount. There were a few loan options presented, and the membership voted on it. [Editor’s note: The board chose from two $2.4M ten-year loan options.]
Did the loan cover the entire project, or did you also ask for contributions from members?
SD: Yes and no. We had to ask for contributions from members [in the form of assessments] because the reserves were drained over the years due to internal issues like plumbing failures. I don’t think you can solely blame the assessments on the façade project, though. We took out a loan with an option for an extra line of credit that we could tap into, which we did. We didn’t want to increase costs, but there were a few unforeseen issues, like fire escapes that needed to be added and some extra masonry work. It was the right time to handle everything. We didn’t want to hire another architect down the road, which would’ve been three times as expensive. So we did as much as we could while we had the resources.
Has the project’s completion made a difference in your day-to-day life? I imagine it might be warmer now in your apartment.
SD: Yes, for sure. I think several members noticed it. Since we were also able to tweak the boiler, I barely need to turn on my radiators now unless the temperature is really, really cold. The building overall is retaining more heat, I think, with all the insulation. The water intrusion issue is gone, which was a huge part of why we started this project. It’s made a massive difference because so many other problems stemmed from that.
MW: [This project] just looked like a smart thing to do as far as ongoing maintenance, because masonry walls are always going to need maintenance, and this would really knock down that cycle because it’s a very durable repair.
But energy efficiency was also a huge part of it — reducing the cost of running the building. I did the fuel savings calculations last year, and even with a much colder winter, we’re using about 20% less.
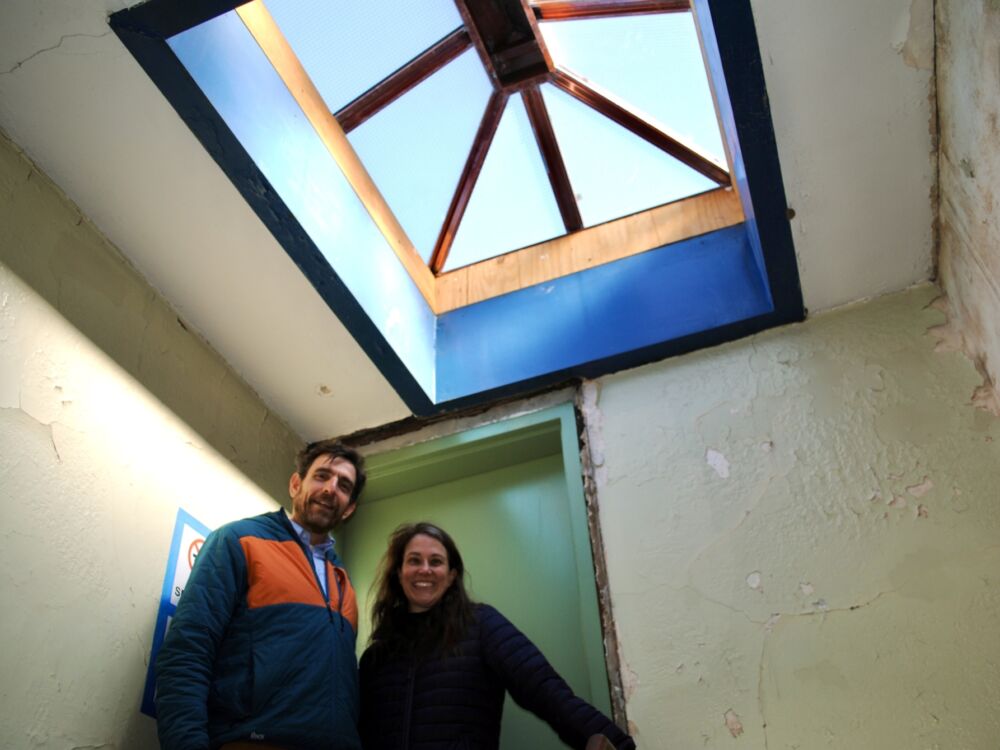
Doucette and Weiss pose under a reinforced bulkhead. Photo: Hannah Berman
How would you advise other people who are maybe being forced to take action and decarbonize their buildings, but they don’t know where to start, or are hesitant to get going?
SD: Don’t do it… I’m just kidding. No, I mean, look, if we could do it, anyone could do it. That’s really the message. I’m a hotel salesperson — now, I know more about lintels and brick than I ever thought I would.
MW: I guess it’s also just finding the right people, right? Designers, architects, or contractors who can offer good guidance — that’s key.
SD: Yeah, finding good people. I mean, it’s like a ballet. It wasn’t just a construction project; it affected our insurance, our operations. It impacted all aspects of running the building. For buildings that already have management companies, it’d be much easier. You still have to make decisions as a board, but some of the logistics and small stuff that we got caught up in, which was really cumbersome, could be handled by them.
For buildings to start saving… I think that’s another thing. We were really conservative on our maintenance. Start planning ahead, getting that financial groundwork in place so that when the hard decisions come up, you’re not panicking. It was stressful — thinking, “This is a big ask of the people I live with.” But if you can lighten that load, it helps.
If we hadn’t done this, we would be in really bad shape for a lot of reasons. I think it can seem really daunting, but we just had to rip the band-aid off and move forward. We had a very motivated board. We lamented many times when it got tough, but it was very rewarding, too, to see it all come together.