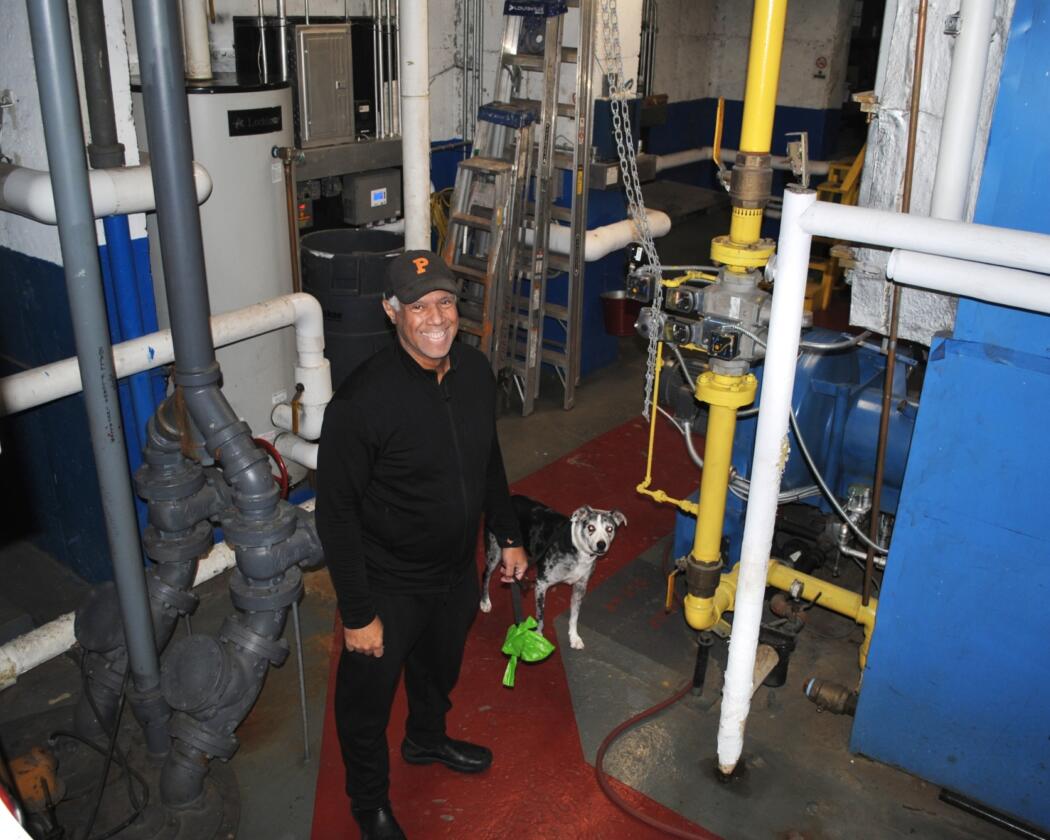
“Read the F*cking Manual!”
A Q&A with Chris McGinnis, a former IBM worker and longtime co-op resident who made it his mission to learn how buildings work so he could make his own more efficient
Chris McGinnis in the boiler room at Two Charlton Owners Corp. Photo: Hannah Berman
Chris McGinnis is a former IBM systems engineer who has lived at Two Charlton Owners Corp, a 16-story co-op in SoHo, for the past 35 years. After getting inspired by his younger sister, who worked in battery sales, he decided to learn more about how electricity can be a cleaner energy source for entire building systems; soon, his newfound passion transitioned into an interest in decarbonizing his own home.
Since then, McGinnis has led his building through a series of efficiency upgrades, starting off small with LED bulbs, submetering, and radiator covers, then moving on to bigger fixes like helping the boiler run more efficiently, upgrading the electrical room, and installing charging stations for electric vehicles in the co-op’s garage.
Skylight sat down with Chris to talk about his detail-oriented process, and how his work mantra — “Read the F*cking Manual” — has guided him through implementing change in his building.
This interview has been edited and condensed for clarity.

Chris McGinnis and his dog Juno in the upgraded electrical room at Two Charlton Owners Corp. Photo: Hannah Berman
Skylight: To start, will you tell us a little bit about your building, and your relationship with it?
Chris McGinnis: Our building was commissioned in 1966. It’s got 176 units. It’s 16 stories above ground, one story below ground. It’s a combination of studios, one-bedrooms, and two-bedrooms. I moved in with my wife, or my girlfriend at the time, in 1990, and then we got married four years later. We had a son in ‘96, and then in ‘97, we moved upstairs — we bought 6L and 6M, and then combined them. After all the combinations, there are 150 apartments.
What kind of energy powers your building?
We’re a two-pipe steam building with two gigantic firebox boilers in our basement that generate steam. We’ve done many upgrades. [The boilers are] dual fuel, meaning we have a 10,000-gallon oil tank and low-pressure natural gas. We typically run off natural gas since it’s more cost-effective, but if our booster takes a hit, we can flip to oil. We’ve done a lot of work to maintain those boilers because heating is a major priority.
Our cooling comes from air conditioners — specifically, a through-wall air conditioning system where you just slide an A/C unit into it. During the winter, our domestic hot water comes from our boilers, which have coils to heat the water. In the summer, we use a Camus system with water tanks. Under high demand, we can also feed hot water directly from the Camus alongside the tanks, though that almost never happens.
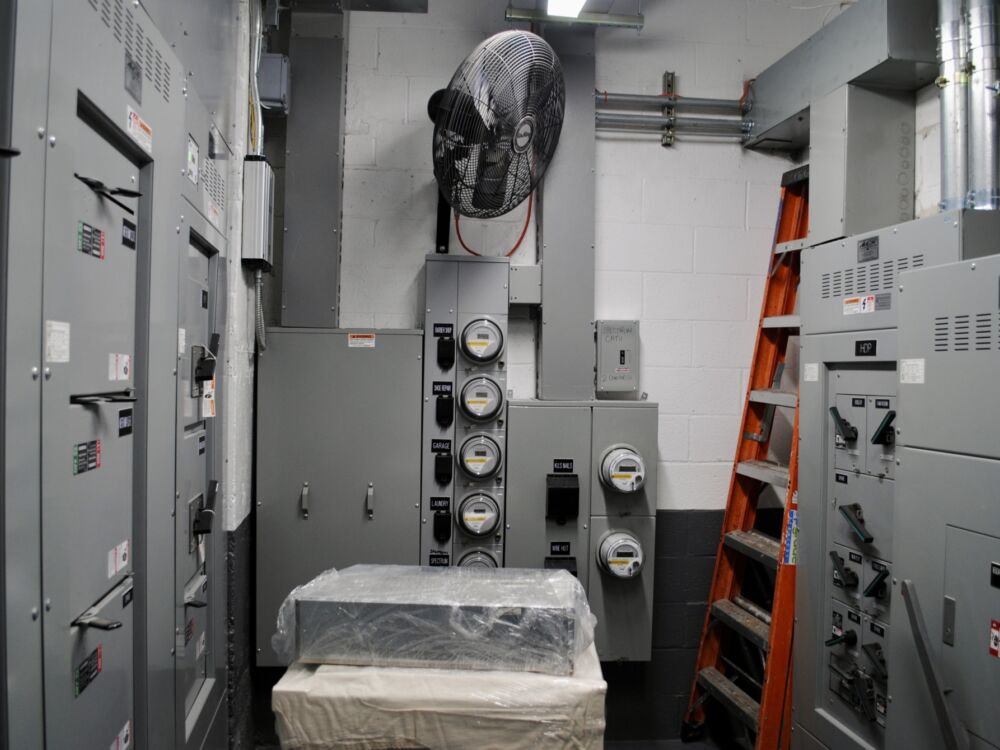
Upgraded electrical room at Two Charlton Owners Corp. Photo: Hannah Berman
Was your involvement in retrofitting motivated by your relationship to the Passive House movement and getting interested in how energy works in buildings, or was there some other reason?
That’s a very insightful question. So the reason I became interested in electricity and stuff in general is my little sister, who’s 16 years younger than me. She was one of the top battery salespeople in the world. She was phenomenal. I come from an IBM background, so I knew tech. I wanted to be able to communicate with my battery geek‑y sister, so I had to learn [about] power stuff. And then as I started talking to her about electricity, I realized, “Oh, I can learn this, because it’s kind of like tech.”
The way I do things is RTFM — Read the F*cking Manual. I download the manual, read it, learn how it works, then figure it out. Then I ask questions like, “Oh, this is how you were going to set this up, but shouldn’t we be doing it this way?” I constantly do that.
I believe in reading the manuals because even with the best teams, if you read things in detail, you’ll pick up nuances and be able to ask the right questions. Understanding the technical details allows me to manage projects better and ensure quality. It’s hard to manage things that you have no clue about at all.
The more I dove in, the more I became interested. One thing led to another, and I really wanted to have an impact.
Then I started investing in real estate, which is a family business. So I was asking friends, like, “What’s the best way of building properties?” Then that turned me onto Passive House. [Editor’s note: the Passive House movement is an approach to residential construction that achieves energy efficiency by insulating a building’s exterior including roof, walls, and windows, to maintain a consistent temperature and reduce energy use. The movement, which started in Germany, has since informed architecture across the world.]
How did your building decide what to attack first, in terms of decarbonizing?
We’ve tried to approach decarbonization strategically. One of the first projects was replacing hallway lighting. We had 152 fixtures with compact fluorescent bulbs (CFLs) that used 37 watts each. We replaced them with LEDs that use just 3 watts per fixture on average. The LEDs have proximity sensors that throttle from 30% to 100% brightness when someone approaches. By law, we have to provide at least one foot-candle of light to the floor. At 30%, we were compliant, so we kept it there.
I returned to the board about ten years ago, around when I retired, and at the time they were considering new burners and boilers. When you ask a company that sells boilers if you need a new one, the answer is always yes. But we had [engineer and energy efficiency specialist] Henry Gifford assess ours, and he said our existing boilers were already 83% efficient, while the new ones were 84%. Spending three-quarters of a million dollars for a 1% efficiency gain didn’t make sense. Instead, we focused on better maintenance. We ended up hiring a new team to do the boiler maintenance. And they’ve been phenomenal. Now our boilers are about 87% efficient.
We also started analyzing our building’s [electrical] energy use even before Local Law 97 (LL97). I took a Passive House training years ago and met an architect, Ben Southworth, who introduced me to his brother, McGowan Southworth. [Editor’s note: Southworth is the co-founder and president of Daisy Chain, a company that assists multifamily buildings with decarbonization and LL97 compliance.]
McGowan had been working on solar energy projects in his building in Sunset Park, and discovered that adding a master meter with sub-meters would have made the system even better. If a building is already direct-metered, you can swap out existing meters for third-party meters that integrate into a centralized system.
So in 2018, I convinced my board to install an electrical meter in our building’s electrical room, monitoring all major power consumption points. We used a Leviton box, which incorporated a Triacta meter. This allowed us to track and analyze power usage at a detailed level. So prior to Local Law 97, we were already on this.
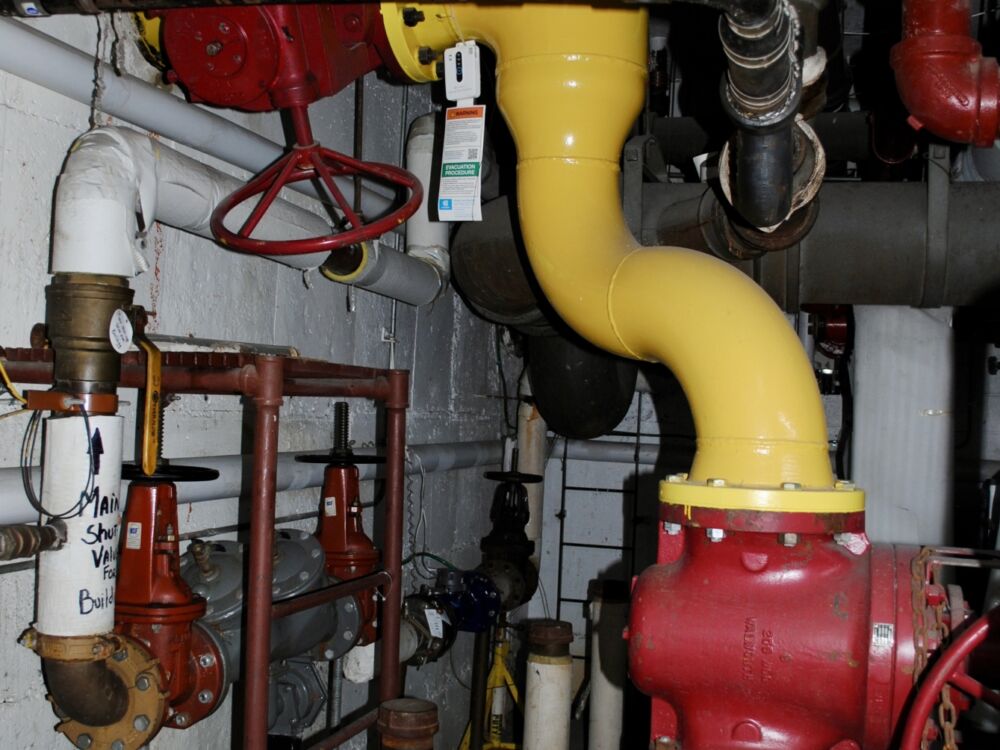
Methane (natural gas) service pipes at Two Charlton Owners Corp. Photo: Hannah Berman
It’s very hard, it seems, to make a plan for a solution when you’re getting contrasting advice from different places. This goes back to your comment about the boiler guy who says, “Get a new boiler,” when in fact a replacement wouldn’t offer much of an improvement. So I’m really curious how you decided who to trust with these projects. What made that decision for you?
What I seek is truth-tellers: People who have real knowledge, and want to engage. The truth-tellers don’t know everything, but they will tell you that. They also tend to be very good at what they do.
Our electricians, Response Electric, have a leader named Reaz Mohammed. He and I would talk in the mornings, sometimes at 5 or 6 AM for an hour, just talking things through. He wants to get it right from the beginning. Response Electric is one of maybe four companies in the city that can revamp your electrical room without ever taking the building down. That means they have to run things in parallel and plan meticulously. If they do it wrong, someone could die, so the stakes are high.
A lot of it comes down to knowing the details, understanding how things flow, and having a team that wants to work with you, not just say things like, “Yeah, yeah, yeah, whatever. We’re gonna just do whatever we want.”
How did you convince everyone else in your building to get on board with the vendors that you have vetted and determined safe to work with?
In 2018 or so, we had a major electrical problem in the building. An electrician went into the meter closet on the 11th floor and started tugging on almost 60-year-old wires. They arced, blowing up the whole meter closet.
Response Electric came in after the previous company had screwed things up, and they were phenomenal. Within three days, they had three floors back up and running. After that, we gave them our next project — replacing circuit breaker boxes throughout the building, in all but 10 of the units.
They did that project and not one complaint. A total record. I was like, “Wait a minute, you went into every apartment and we had not one complaint? We have people who complain three times a day for nothing!” But they were so professional, and they figured out a bunch of things that were fundamentally wrong with our electrical system, so they rectified all that.
The same goes for McGowan, who helped with our sub-metering system and paperwork for the Public Service Commission. He’s still involved with our future projects, like installing solar on our roof. I won’t do anything major without them because I want to know who’s working in my building and infrastructure.
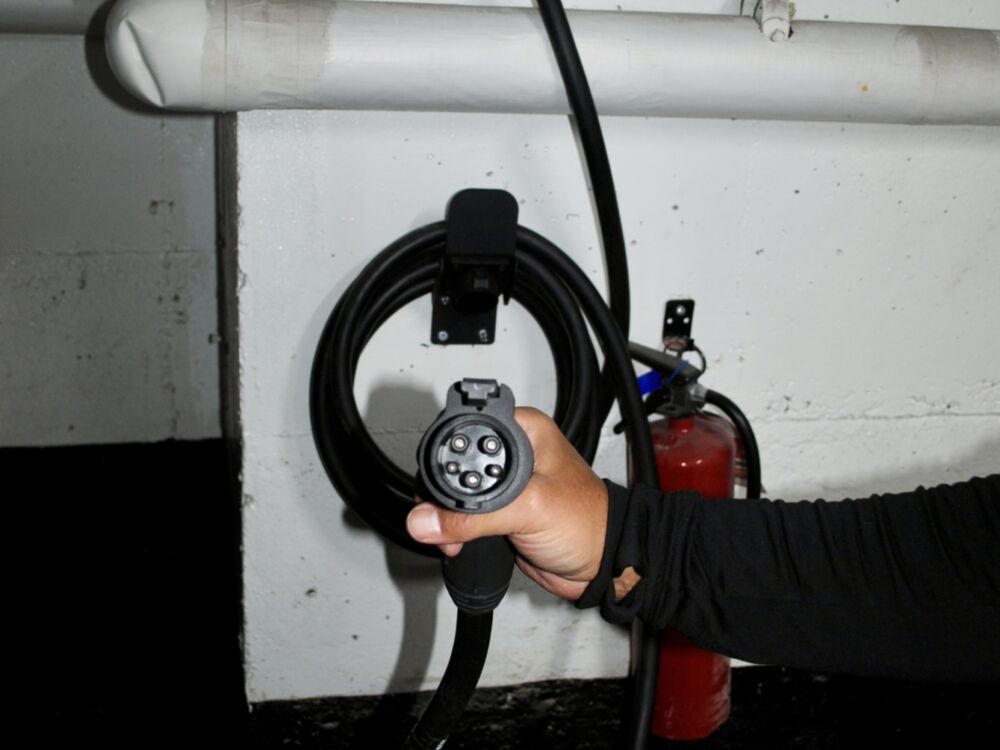
After one project McGinnis oversaw, there are now 38 EV chargers in the garage of Two Charlton Owners Corp. Photo: Hannah Berman
Tell me a little bit more about the financing. I know you mentioned NYSERDA was helping with incentives, but how did you finance all these projects?
NYSERDA, Con Edison, and other organizations publish incentive programs, so every year, I check in with contacts at Con Ed to get the most recent plans. Often, engineering or electrical companies will handle the paperwork for incentives, or we’ll hire a specialist. McGowan, for example, became an expert in financing through his experience as a co-op president. He figured out how [we could] combine subsidies, tax relief, and IRA benefits to maximize savings.
For the specific projects you’ve taken on, have all of them been net zero cost due to incentives, or have you used reserve funds?
Almost none of them are net cost zero, but they all have an acceptable payback period. For example, when we installed thermal enclosures — cozies — on our convectors, the payback period was about three to four years.
I ask because financing is usually such a big concern for people considering large-scale upgrades. How much did each unit have to contribute?
Almost everything I’ve talked about came out of our capital reserves. We have two different bank accounts: An operating account, and a capital account. We try to keep at least a million dollars in our capital account, and then we have at least a million-dollar line of credit. And then for projects that are bigger than that, every 10 years or so, we have to do an assessment.
We try to run in such a way that we are growing the capital in our capital account. We do that by making investments [in projects like decarbonization improvements] which drive down our operating expense — we try to be in a position where we’re running our building at a lower cost than everybody else.
I think you’ve already thrown out a lot of great advice, but do you have any specific advice for others who are hesitating to take action towards retrofitting their own buildings?
A lot will just depend on the specifics. But I would say that really what’s needed, in my opinion, is diligence. If somebody is just willing to be diligent — they don’t have to do what I do to the extent that I do — but you have to figure out a way of finding trusted teams. There’s plenty of really good people out there, but there’s lots of scoundrels. If you get in bed with a scoundrel, nothing good is going to happen from that.
We’ve spent a lot of time vetting and figuring out that Kelvin (formerly Radiator Labs) is really good. Do projects with Kelvin! We figured out that Response Electric is really good; do electrical work with Response Electric! They’re going to get it done, and it will work. Daisy Chain, founded by McGowan Southworth, knows their way around electricity and sub-metering and solar.
Follow the path.